|
Monday, February 10, 2014
A Dedicated Sharpening Bench part 6
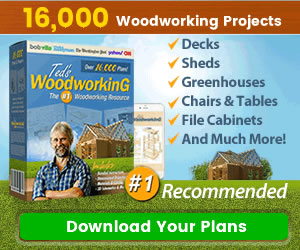

With the frame assembly dry fit and the bench surface placed into the leg joinery, I carefully place the granite insert on top to establish its permanent location. My initial thoughts were to install it off to one side but after laying it on the work surface and imagining how it would function in daily use, I decided to center it. This decision was based on the under carriage bracing system and the drawer hanger locations. I also felt that it would be more comfortable centered while in use and may keep the bench a little more balanced. So now that I know where I want to place it I carefully lay out and scribe around the perimeter.

Once I have the lay out complete its time to start thinking about just how Im going to make this cut-out! My first thought is to use my frame saw and after drilling a pilot hole through the oak, dis-assemble the saw and thread the blade through the opening as you would on a scroll saw. I proceeded to do this and made the first long rip cut down the front of the piece but hit a wall when faced with the cross cuts. The frame saw only has a 6" throat so it wouldnt work for the cross cutting. 1" oak is a challenge at the best of times and the light blade of the frame saw was really pushing it. I decide to use my Japanese ryoba saw, this is the one without a back and has both a rip and cross cut tooth configuration. I use a brace and bit and bore a series of holes along the cut line to fit the ryoba and get things underway. In the next shot you can see the first rip cut at the rear and the holes drilled to allow the blade of the ryoba to pass through.

In a power tool shop this procedure wouldnt be a big deal, maybe a jig saw would suffice or even a table saw with the piece placed over the blade and then carefully raising it up through the work. In my shop however, a little trial and error and Ill have the cut out complete. The ryoba works its way through the oak. Some people have a hard time with pull saws binding and teeth breaking but if you dont force the cut and let the saw do the sawing, even on this hard white oak its a relatively easy task.

Its not pretty but it worked! Ill clean up the inside edges next.

Again with a nice wide chisel I carefully work my way around the area taking small bites. I begin from the underside and chop down a little more than half way. I flip the piece over and finish the job from the top where its seen. I have a corner chisel and this is a perfect application for it. These are a kind of specialty item that you could indeed live without but they do come in handy from time to time.

I dry fit the granite and note any tight spots along the edges. I mark them and remove the slab to slowly and carefully pare away the fat to achieve a perfect fit.

Now that I have the surface cut-out complete I turn my attention back down to the frame and dimension the final rear stretcher. This 2" oak is placed at the rear top and the back of the work surface will sit on it when complete. So again with the mortise chisel I chop out the cavity.

The tenons in the oak are off set to allow for the dado Ill plough out next. This groove will hold the under carriage cross pieces, both the granite insert supports as well as some drawer hangers.

My plough plane is the perfect tool for the job.

With the frame joinery finally complete, Ill start to lay out the components for the granite supports. These are made from some hardwood offcuts I had, in this case some birch and walnut and I dimension them so that when installed the granite will sit slightly proud of the surface. When I say slightly proud, I mean no more than the thickness of a standard sheet of writing paper. The back of the supports will sit in the dado we just cut into the top, rear stretcher and the front will be screwed and joined into two recesses on the underside of the front apron.
I begin as usual by laying these out.

I approach this like I would with chopping a half blind dovetail, clearly scribing the edges and the depth of the cavity. The main difference between this and a dovetail is the dovetail is usually chopped into the end grain of a board while this is running along the grain. Care must be taken to insure I dont chop too deep and split the piece. I begin my making some saw cuts to establish the outer edges and then with a chisel begin removing the waste.

In a power tool shop this procedure could be easily accomplished with a router and a jig so with that in mind Ill get mine to complete the cut-out.

Gotcha! Did you really think my router would have a plug attached? Taking shallow passes, I work my way down with the router plane until I reach my desired depth.

Then with a chisel I clean up the corners and dry fit the supports. Im looking for a nice tight fit- how tight? With the apron clamped in my face vise Im able to press the supports down into the openings and with out any support theyre able to sit proud without sagging or falling out.

Ill re-assemble the bench top pieces and dry fit the granite supports.

When Im happy with the fit and the depth of the components are well established, Ill take my awl and mark for some screw holes. I need to make all of these pieces removable for times when I want to re-surface the bench top. This is also why the front cross member on the tool tray is also removable. My vintage hand drill with a modern counter sink bit enables me to drill and countersink in one pass.

From here I begin laying out and measuring for the drawer hangers. They will also sit in the rear apron dado and are cut for a snug fit. The two inner hangers will need to be shaped to fit around the profile of the granite. I approach this as I did when removing the waste on the underside of the feet. I make a series of saw cuts to establish the depth and then chisel out the waste.

In the next shot you can see the shaped drawer hanger in the fore ground and the side example in the rear. These will also recieve a dado for the drawers to hang in.

To add some added insurance that all of these pieces do what Im hoping theyll do (and thats holding a heavy granite slab and two drawers tightly to the bottom of my workbench) Ill add some pocket hole screws that will secure it up into the bench top. A pocket hole jig is a useful tool in the hand tool woodshop but is usually associated with power tools.

Here, with a special bit chucked into my brace I can easily drill the holes and am ready for a final dry fit. You may notice at this point I only had two of the four drawer hangers installed; truth be told I wanted to see if this system would work and when it did I went back and made the two for the left hand drawer.

I was planning on showing the frame glue up in this post but looking at its length I think Ill save it for the next one-
cheers!
Subscribe to:
Post Comments (Atom)
No comments:
Post a Comment